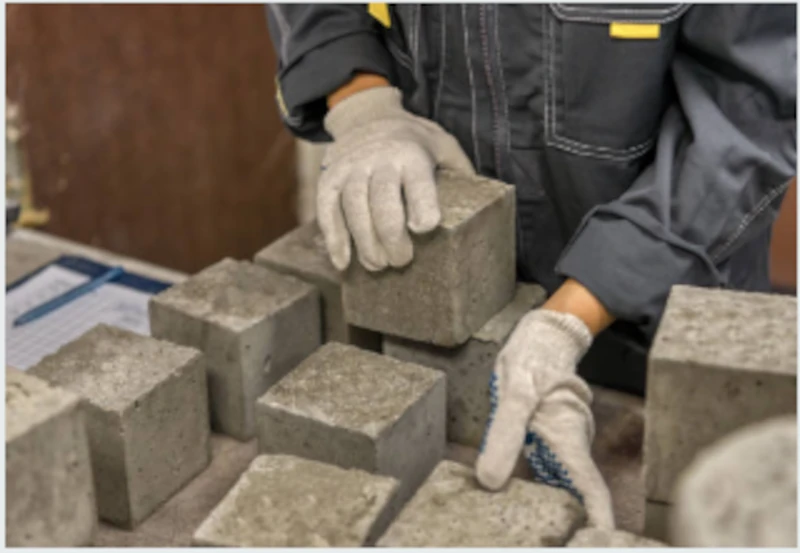
Concrete Curing in 2025: Best Practices, Sustainability, and the Science Behind Stronger Structures
In the world of construction, concrete remains one of the most critical materials. It is the backbone of roads, buildings, bridges, dams, and virtually every type of infrastructure. But pouring concrete is only half the job, ensuring it cures properly is what determines its long-term strength, durability, and performance. Concrete curing, the process of maintaining adequate moisture, temperature, and time after placement, is evolving with sustainability, science, and technology at the forefront in 2025.
This in-depth guide explores the fundamentals of concrete curing, modern advancements in curing techniques, its environmental implications, and the best practices construction professionals must adopt to deliver high-performance concrete in an eco-conscious era.
What Is Concrete Curing?
Concrete curing is the controlled process of maintaining appropriate moisture, temperature, and timing conditions to allow cement hydration to continue after concrete is placed and finished. This hydration process is the chemical reaction between cement and water that gives concrete its strength and durability.
The main objectives of curing are:
- To prevent rapid moisture loss from the concrete surface, especially during hot or windy conditions.
- To regulate the temperature of concrete during the early stages of hydration.
- To allow time for the concrete to gain enough strength to support loads and resist damage.
Neglecting proper curing can lead to premature drying, cracking, dusting, and significantly reduced structural strength. That’s why curing is considered a critical component of quality control in any concrete application.
Curing also plays a major role in protecting against long-term issues such as:
- Efflorescence, a whitish deposit caused by water-soluble salts
- Carbonation, where CO₂ penetrates the concrete and lowers pH
- Freeze-thaw damage, especially in climates with seasonal cycles
These problems can severely compromise concrete integrity and aesthetics over time. Moreover, improperly cured concrete may delaminate or fail to bond well with coatings or overlays, leading to higher maintenance costs in the future. Even in decorative applications such as polished concrete floors, poor curing can lead to discoloration or inconsistent finishes.
Why Curing Matters More Than Ever in 2025
Concrete structures in 2025 are expected to meet higher performance, sustainability, and durability standards than ever before. From high-rise smart buildings to eco-friendly infrastructure, ensuring long-lasting concrete performance is a key responsibility.
As sustainability becomes a driving force in construction, contractors must balance the need for performance with eco-conscious choices. Additionally, modern concrete mixes often include supplementary cementitious materials (SCMs) such as fly ash, slag, or silica fume that enhance sustainability but require more careful curing practices due to slower hydration.
Regulatory pressure is also increasing. Many countries have adopted carbon neutrality targets for infrastructure. Poor curing can lead to reduced service life, requiring more frequent repairs or reconstruction, which contributes to carbon emissions and costs.
Construction timelines are also tighter. Any early damage due to poor curing can lead to costly delays, repairs, or even structural failures. These risks make it crucial for modern construction teams to integrate curing planning into the core project strategy.
Improved curing also results in reduced maintenance over time. A properly cured surface is less prone to cracking, spalling, and discoloration, preserving the integrity and appearance of the structure. As urbanization continues to accelerate globally, especially in emerging markets, the demand for reliable, long-lasting infrastructure built with strong concrete is growing.
Moreover, investor and client expectations now extend beyond basic durability. Stakeholders want performance metrics, green building certifications, and lifecycle data. Proper curing is foundational to achieving these expectations, making it a point of strategic importance for competitive firms.
Methods of Concrete Curing
There are several widely accepted methods of curing, each chosen based on the environment, type of concrete, and specific project needs.
1. Water Curing
Water curing is one of the oldest and most effective methods. It involves keeping the concrete surface moist by:
- Ponding: Covering the surface with water to create a shallow pool. Ideal for horizontal surfaces like floors and slabs.
- Sprinkling: Regular application of water through sprinklers or hoses.
- Wet coverings: Using soaked burlap, cotton mats, or hessian to retain moisture.
This method ensures constant hydration and prevents surface drying, but it can consume a large amount of water and require significant labor. In 2025, many contractors recycle graywater or use smart sprinklers that minimize waste.
Water curing remains the gold standard when maximum strength is required, especially for critical infrastructure such as bridges, airports, and dams. However, due to climate change and rising water scarcity, contractors must often adapt or combine techniques to balance performance and environmental constraints.
Recent innovations have also introduced moisture-retaining polymers and hydrogels that retain water for extended periods. These can be incorporated into wet coverings or applied directly to surfaces, making traditional water curing more efficient and environmentally friendly.
2. Membrane Curing
Membrane-forming curing compounds are sprayed or rolled onto freshly placed concrete. These compounds form a thin, waterproof film that locks moisture inside.
- Efficient in large-scale or remote projects
- Reduces water waste and human effort
- Requires clean surfaces for optimal adhesion
These compounds are now available in biodegradable or water-based options that comply with environmental guidelines. They are frequently used in road construction, parking decks, and commercial developments where water curing may be impractical or costly.
Proper application techniques are vital. Uneven spraying can lead to dry spots, which compromise hydration. Workers must be trained in correct equipment usage, application timing, and surface preparation.
The latest membrane curing technologies also offer UV resistance, allowing concrete to be protected from harmful solar radiation that can accelerate drying. Some products are even designed to biodegrade over time, reducing post-construction cleanup and environmental impact.
3. Steam Curing
Steam curing accelerates strength development by maintaining high humidity and elevated temperature. Common in precast concrete plants, it involves:
- Controlled chambers or enclosures
- Specific temperature and timing schedules
- Faster curing cycles, ideal for production lines
However, it consumes energy and requires specialized equipment, making it less common on traditional job sites. Advances in low-emission boilers and renewable-powered heating are making this option more eco-friendly.
In precast environments, steam curing allows daily casting and demolding, boosting productivity. This efficiency makes it a vital component of modern modular and prefabricated construction methods.
Steam curing also allows for greater quality consistency across products. Since conditions are tightly controlled, there is less variability in strength and finish between units, which is critical in high-volume production environments like infrastructure beams and precast façade panels.
4. Internal Curing
Internal curing involves adding pre-saturated lightweight aggregates or superabsorbent polymers into the concrete mix. These materials slowly release water over time, supporting hydration from within.
Useful for high-performance and low water-cement ratio concretes
Reduces autogenous shrinkage
Promotes uniform strength development
Internal curing is especially useful for bridge decks, high-rise buildings, and structures exposed to extreme weather conditions. It eliminates the need for surface curing, reducing dependency on external water sources.
As research continues, new internal curing agents are being developed using nanotechnology and biodegradable gels to optimize performance and sustainability.
In 2025, internal curing is also being paired with predictive AI models. These platforms use real-time hydration data and environmental sensors to adjust mix designs or recommend curing durations, ensuring optimal results every time.
5. Insulated and Heated Blankets
Insulated blankets are used to cover concrete in cold weather to maintain hydration-friendly temperatures. Some blankets even have embedded heating elements.
- Helps avoid thermal shock and freeze damage
- Allows continued curing in sub-zero conditions
- Enhances curing efficiency on large exterior pours
The latest models use smart sensors to automatically adjust heating levels based on real-time temperature feedback. They are commonly used in northern climates and during winter builds.
These blankets can now be connected to cloud-based monitoring systems, enabling remote control and data logging. This is particularly valuable on projects where consistent temperature control is critical to meeting strict strength or schedule milestones.
Smart Curing and IoT Integration
In 2025, digital transformation is revolutionizing how curing is monitored and controlled. Smart sensors and Internet of Things (IoT) devices are being embedded directly into concrete structures or formworks to gather real-time data on moisture levels, internal temperatures, and hydration progress.
These smart curing systems offer numerous benefits:
- Automated alerts if curing conditions fall outside optimal ranges
- Historical data for quality assurance and audit trails
- Remote monitoring via mobile apps and dashboards
With real-time feedback, project managers can adjust schedules, heating systems, or water application strategies to ensure ideal curing even under shifting environmental conditions.
AI and machine learning algorithms are also being integrated into curing platforms to predict outcomes based on current data, weather forecasts, and material specifications. These systems help contractors optimize both timing and methods, reducing guesswork and improving consistency across different job sites.
Platforms like PrecisionSpan now integrate curing analytics directly into construction management workflows, allowing seamless communication between field sensors, equipment, and supervisory teams.
Sustainability and Environmental Considerations in Curing
As the industry shifts toward sustainable construction practices, curing methods must adapt to reduce water waste, lower energy consumption, and support green building certifications such as LEED and BREEAM.
Here’s how concrete curing is evolving to meet environmental goals:
Water Conservation
- Use of graywater or recycled water for curing tasks
- Adoption of low-volume misting systems and smart sprinklers
- Combining curing with rainwater harvesting systems to reduce potable water use
Reduced Carbon Footprint
- Integrating low-emission steam systems powered by solar or biofuels
- Promoting membrane curing as an alternative to intensive water usage
- Leveraging internal curing to eliminate external resource demand
Material Innovation
- Use of bio-based curing agents and coatings
- Development of photodegradable membranes
- Nanomaterials that require less energy to activate hydration
Curing is increasingly being assessed as part of a building’s overall environmental profile. Accurate reporting of curing-related emissions, water use, and energy consumption helps firms qualify for tax incentives, certifications, and investor scrutiny.
Best Practices for Concrete Curing in 2025
Achieving optimal concrete performance requires a proactive curing strategy tailored to the project’s environmental conditions, mix design, and performance goals.
Pre-Pour Planning
- Include curing strategy in project scope and schedule
- Choose curing method based on site conditions, material mix, and timeline
- Procure equipment and personnel before concrete placement
During Curing
- Monitor environmental conditions (temperature, humidity, wind)
- Use sensors or manual inspections to verify moisture retention
- Keep curing uninterrupted for a minimum of 7 days (or as per specifications)
Post-Curing Assessment
- Conduct compressive strength testing
- Inspect for surface defects like cracking or discoloration
- Document curing practices for quality records and certification audits
Firms that invest in training their teams on proper curing procedures enjoy reduced defect rates, increased client satisfaction, and improved compliance with sustainability standards.
Challenges and Common Mistakes in Curing
Despite technological advances, many curing errors still occur on job sites:
- Premature removal of curing blankets or membranes, especially in hot climates
- Insufficient water curing during weekends or holidays
- Poor application of curing compounds, resulting in uneven moisture retention
- Neglecting to monitor weather forecasts, leading to unexpected temperature drops or rain
These mistakes not only reduce performance but also increase the risk of litigation, project delays, and rework. Training, supervision, and technology are all critical to preventing such issues.
In many cases, poor curing stems from a lack of communication between design teams and construction crews. Ensuring curing requirements are clearly specified in the construction documents and revisited during preconstruction meetings, can bridge this gap.
Innovations on the Horizon
Concrete curing is a centuries-old practice, but innovation is accelerating rapidly. In the coming years, expect to see:
- Self-healing concrete that reduces the need for perfect curing
- AI-curated curing schedules based on real-time environmental and material data
- Automated drones that spray water or compounds over large slabs
- Digital twin integrations that simulate curing before a pour even begins
Companies like PrecisionSpan are leading the way by developing platforms that unify planning, execution, and data analysis, making curing more transparent and effective than ever before.
Conclusion: Investing in Stronger, Greener Structures
In 2025, concrete curing is no longer just a post-pour formality, it is a vital component of sustainable, long-lasting construction. As performance standards rise and sustainability becomes central to project success, proper curing ensures that your concrete not only stands strong today but remains reliable for decades.
Whether you're using internal curing, smart blankets, AI monitoring, or traditional water curing, the key is consistency, science-backed techniques, and strategic integration into your construction workflow.
PrecisionSpan helps construction firms embed best practices into their daily operations, ensuring curing is monitored, managed, and measured effectively.
Ready to build stronger, smarter, and greener?
Book a Demo or Get Started Free with PrecisionSpan today.
0 Comments