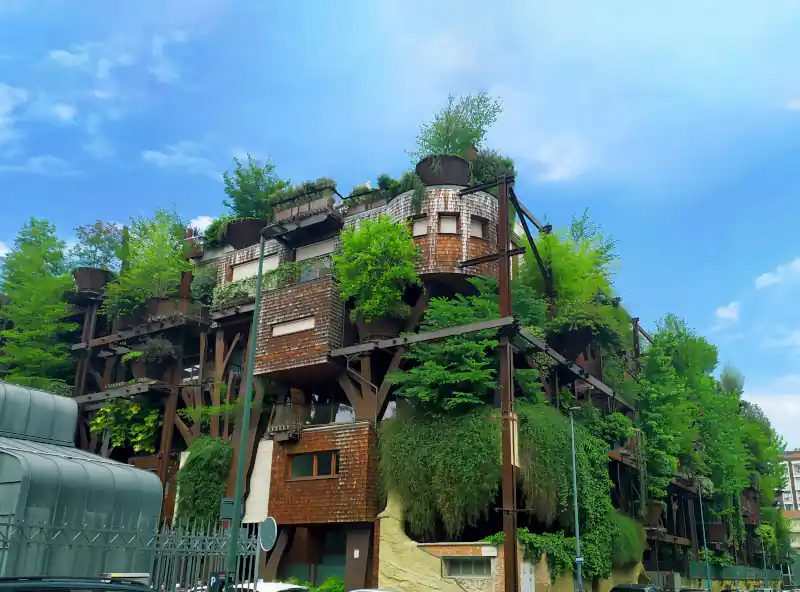
The Future of Sustainable Construction: Trends That Matter in 2025 and Beyond
In 2025, sustainability is no longer a buzzword in the construction industry, it's a requirement. As global awareness of climate change, material scarcity, and environmental impact grows, the pressure on the construction sector to adopt greener practices is intensifying. Governments, clients, and communities are demanding buildings that are not only functional but also environmentally responsible. Construction firms that embrace sustainability are finding themselves more competitive, cost-efficient, and future-ready.
Sustainable construction is the practice of creating structures and using processes that are environmentally responsible and resource-efficient throughout a building’s lifecycle: from siting to design, construction, operation, maintenance, renovation, and demolition. In this blog, we explore the key trends that are shaping the future of sustainable construction in 2025 and beyond.
1. Green Building Certifications Going Mainstream
Certifications like LEED (Leadership in Energy and Environmental Design), BREEAM (Building Research Establishment Environmental Assessment Method), and EDGE (Excellence in Design for Greater Efficiencies) are increasingly becoming standard requirements for new buildings. In 2025, more countries are adopting national mandates requiring public infrastructure and government-funded projects to meet minimum green certification levels.
The shift toward green certification is being driven by both environmental policy and economic logic. Certified buildings tend to consume less energy and water, use materials more efficiently, and provide healthier indoor environments, all factors that reduce operating costs. More importantly, investors and real estate buyers are now evaluating green certifications as a mark of asset value and longevity.
PrecisionSpan allows construction teams to monitor sustainability compliance metrics in real-time, ensuring alignment with certification standards across every phase of the project.
Architects are now integrating sustainability into the earliest phases of design, using energy modeling and simulations to meet certification goals. Engineers are choosing systems and materials that align with energy, water, and indoor environmental quality standards. The result is a truly integrated design and construction process that delivers more value to stakeholders.
2. Eco-Friendly and Recyclable Materials
Traditional construction materials like concrete, steel, and asphalt have high carbon footprints due to energy-intensive manufacturing processes. The industry is increasingly turning to sustainable alternatives:
- Cross-Laminated Timber (CLT): Engineered wood products that are renewable, lightweight, and sequester carbon.
- Recycled Steel: Reduces the need for virgin material and minimizes environmental degradation.
- Hempcrete and Mycelium Bricks: Naturally derived, biodegradable, and thermally efficient materials gaining ground in residential and low-rise construction.
By 2025, more than 20% of new builds in developed nations are expected to use at least one recycled or bio-based material. Platforms like PrecisionSpan help contractors track sourcing certifications and compliance with environmental standards for all materials used.
There's also growing innovation in bio-based insulation, recycled glass tiles, and carbon-capturing cement technologies. As the demand for green buildings increases, suppliers are investing in the research and development of sustainable alternatives to meet regulatory and consumer demand.
Builders are also becoming more selective about their suppliers, opting for vendors who provide Environmental Product Declarations (EPDs). These documents help quantify the environmental impacts of materials and provide the data needed for better decision-making. This shift also incentivizes manufacturers to improve their production methods, creating a virtuous cycle of sustainability across the supply chain.
3. Energy-Efficient Design and Net-Zero Buildings
The move toward net-zero energy buildings, structures that produce as much energy as they consume, is picking up speed. Governments in the EU, US, and parts of Asia are rolling out tighter regulations and incentives for net-zero construction.
Innovative design practices such as passive solar orientation, double-skin façades, green roofs, and energy modeling are becoming essential. Smart HVAC systems, automated lighting, and high-performance insulation reduce energy use while maintaining occupant comfort.
Solar integration is also evolving. Building-integrated photovoltaics (BIPV), where solar panels are built directly into façades or windows, are increasingly popular for commercial and high-end residential projects.
PrecisionSpan integrates with building performance analytics tools, helping construction teams validate energy targets and adjust strategies dynamically.
Net-zero goals are also impacting the choice of construction site and orientation. Urban infill developments are being prioritized to reduce commute emissions, and orientation strategies are leveraging natural light and ventilation more than ever before. Building commissioning has become a crucial step to verify energy performance before occupancy.
These buildings also benefit from energy storage technologies such as lithium-ion and saltwater batteries. Storing excess solar energy for use during peak times improves energy self-reliance and reduces strain on public grids. Smart grid integration allows buildings to sell energy back to the grid, further enhancing cost efficiency and sustainability.
4. Water Conservation and On-Site Recycling
Water scarcity is a growing concern in urban development. In response, sustainable construction now emphasizes water-efficient fixtures, rainwater harvesting systems, and on-site graywater recycling.
Technologies like smart irrigation, low-flow plumbing, and stormwater management systems are being specified at the design stage. LEED and similar certifications now allocate specific points for innovative water management solutions.
Construction sites are also being redesigned to reduce water usage during construction activities. Pressure-washing alternatives, modular prefab construction, and dry processes (like dry cutting and polishing) are being embraced.
Using PrecisionSpan, construction managers can track water usage metrics in real time, ensuring compliance with sustainability goals and identifying areas for improvement.
The integration of digital twin technology now allows stakeholders to simulate water usage scenarios during early design phases, minimizing risk and maximizing water efficiency strategies. Greywater systems are increasingly common in commercial and residential buildings, repurposing wastewater for landscaping and flushing.
In many cities, construction firms are also collaborating with local utilities to implement district-scale water solutions. These include shared rainwater harvesting systems and centralized treatment units that serve multiple buildings, enhancing efficiency at a community level.
5. Circular Economy and Waste Reduction
The concept of a circular economy, where materials are reused, recycled, and repurposed, is now foundational to sustainable construction. Construction and demolition waste currently account for over 30% of global landfill volumes. That’s changing in 2025.
Modern job sites now feature advanced waste segregation systems, partnerships with recycling firms, and deconstruction planning rather than demolition. Reclaiming materials like steel, wood, and fixtures for reuse is not just eco-conscious, it’s cost-effective.
BIM (Building Information Modeling) and material passports (digital records of material composition and reuse potential) are enabling better waste tracking and reuse logistics.
PrecisionSpan supports circular practices by integrating material reuse tracking and providing automated alerts when waste targets exceed benchmarks.
Manufacturers are now labeling materials with QR codes linked to material passports, making it easier for future demolition crews to reclaim and repurpose materials. Companies are creating marketplaces to trade surplus materials, reducing waste and enabling circular transactions.
Another emerging trend is designing for disassembly (DfD), where buildings are constructed in a way that allows easy dismantling and reuse of components. This method aligns with both economic and environmental goals, offering a strategic path forward for sustainable construction practices.
6. Prefabrication, Modular Construction, and 3D Printing
Modular construction and prefabrication not only speed up project delivery but also reduce material waste and environmental disturbance. Components manufactured off-site in controlled environments result in fewer defects and optimized resource usage.
3D printing, especially with sustainable materials, is emerging as a green construction technology. Entire housing units are now being printed using recyclable concrete or biodegradable composites.
These methods minimize site disruptions, cut down transportation emissions, and support better quality control. A McKinsey report estimates modular techniques can reduce construction waste by up to 90%.
PrecisionSpan helps manage off-site manufacturing schedules, delivery logistics, and quality control tracking in modular projects.
3D printing’s potential extends to disaster relief housing, affordable housing, and remote-area construction. Architects and engineers are collaborating with 3D printing firms to design homes optimized for local materials, climate resilience, and reduced carbon output.
Moreover, prefabrication enables consistency and quality in multi-site projects, making it easier to scale sustainable building efforts. For large developers and government projects, it provides an ideal balance between speed, cost, and environmental performance.
7. Smart Technologies for Energy and Resource Management
IoT-enabled sensors and smart meters are revolutionizing how buildings consume resources. In 2025, buildings will increasingly feature:
- Smart lighting systems that adjust based on occupancy and daylight.
- AI-powered HVAC that learns user behavior and optimizes climate control.
- Energy dashboards that allow occupants to monitor and reduce usage in real time.
These technologies lead to substantial operational savings and user empowerment. They also help facilities teams implement predictive maintenance, avoiding energy-wasting failures.
On construction sites, IoT sensors monitor resource use, track machine efficiency, and detect leaks or excess emissions. PrecisionSpan’s platform allows for seamless integration of IoT devices to improve resource management both during construction and post-handover.
Cloud-based analytics platforms are also enabling benchmarking across portfolios, helping firms identify underperforming assets and allocate sustainability investments more effectively.
In addition to efficiency, smart building technologies are enhancing occupant well-being by maintaining optimal air quality, temperature, and lighting conditions. These human-centric features align sustainability with livability, ensuring greater acceptance and satisfaction among end users.
8. Carbon Accounting and Embodied Carbon Reduction
In 2025, construction firms are not just concerned with operational carbon (emissions during building use) but also embodied carbon, the emissions produced throughout the material lifecycle.
Tools like EC3 (Embodied Carbon in Construction Calculator) are used to evaluate the environmental impact of materials from extraction to installation. This data informs procurement decisions and construction practices.
Many contractors are setting carbon budgets and reporting emissions to clients and regulators. Carbon offsets, although sometimes controversial, are also being explored for unavoidable emissions.
PrecisionSpan enables carbon tracking dashboards that summarize both operational and embodied emissions, helping project teams meet sustainability reporting requirements.
Lifecycle carbon analysis is now integrated into early design stages, with real-time tools enabling iterative decisions that optimize both structural efficiency and environmental impact. With carbon neutrality becoming a critical benchmark, firms that fail to address embodied carbon risk regulatory penalties and diminished stakeholder trust.
The construction industry is also exploring carbon-negative materials, those that sequester more carbon than they emit during production. Innovations in algae-based concrete, bioplastics, and carbon-infused aggregates are shaping the next frontier in sustainable building.
9. Sustainable Urban Development and ESG Reporting
Sustainable construction is now part of a broader movement toward sustainable urbanization. Master-planned communities, mixed-use developments, and transit-oriented design (TOD) are shaping city planning.
Construction firms involved in large-scale urban development are also being evaluated based on ESG metrics (Environmental, Social, Governance). Investors, lenders, and clients are requiring disclosures on emissions, labor practices, and social impact.
PrecisionSpan provides ESG-friendly reporting features that allow firms to communicate their sustainability progress effectively and transparently.
Urban development is embracing smart city infrastructure, public Wi-Fi, smart lighting, autonomous shuttles, and green corridors, to improve livability and sustainability. Mixed-use zoning promotes reduced car use and healthier lifestyles.
Governments and municipalities are using ESG ratings to determine project funding and development approvals. This trend makes it essential for contractors and developers to embed ESG principles into every phase, from design to delivery to post-occupancy monitoring.
10. Workforce Training and Green Skills
A sustainable construction future depends on a skilled workforce. In 2025, training programs in green building practices, energy modeling, and material recycling are expanding.
Universities and trade schools are adapting curricula to meet industry demand. Construction firms are investing in upskilling programs and certifications for site workers, engineers, and managers.
By embedding sustainability into professional development, the industry ensures consistent and scalable implementation of green practices.
PrecisionSpan supports this by enabling training modules and compliance tracking for sustainable construction protocols.
Additionally, some contractors are creating green innovation labs where employees can experiment with new tools, materials, and methods. Mentorship programs and partnerships with environmental NGOs are also helping to bridge the skills gap in underserved communities.
Green certifications such as LEED Green Associate and WELL AP are now seen as competitive advantages for professionals at all levels, signaling a commitment to environmental responsibility and modern best practices.
Conclusion: Building a Greener Future Together
Sustainable construction is no longer optional, it’s essential. As we move through 2025 and beyond, the pressure to reduce carbon footprints, manage resources more efficiently, and build responsibly will only increase.
Embracing green building certifications, eco-friendly materials, modular methods, and smart technologies isn’t just good for the planet, it’s smart business. Construction firms that align with sustainability goals are securing more projects, attracting top talent, and gaining investor confidence.
Platforms like PrecisionSpan are empowering builders to meet these goals through real-time data, intelligent scheduling, and integrated sustainability tracking.
From carbon accounting to circular construction, the tools and practices outlined in this blog are setting a new standard for the industry. The construction firms that invest in sustainable innovation today will lead the market tomorrow.
Ready to build the future responsibly?
Book a Demo or Get Started Free and discover how PrecisionSpan helps you meet the challenges and opportunities of sustainable construction in 2025 and beyond.
0 Comments